Record buyer demand means US warehouses are already filling up. : NPR
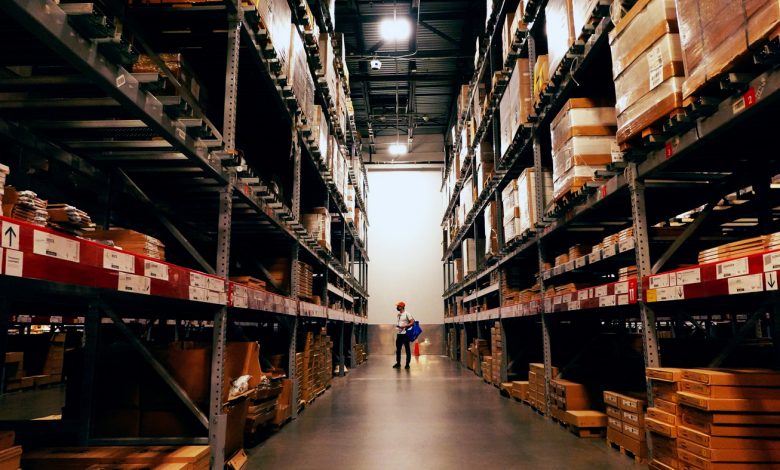

A person walks in the IKEA warehouse in New York City on October 15.
Image of Michael M. Santiago / Getty
hide captions
switch captions
Image of Michael M. Santiago / Getty

A person walks in the IKEA warehouse in New York City on October 15.
Image of Michael M. Santiago / Getty
Doug Kiersey has built, bought, and leased warehouses for nearly 40 years. He had never seen anything like this.
“It’s completely unprecedented,” said Kiersey, president of Dermody Properties, which owns warehouses used by some of the country’s largest retailers. “In some markets…we’re over 99% filled.”
In a word, America’s warehouses are running low. All was declared and boomed at the seams.
How did that happen?
Warehouses have become a central link in the country’s supply chain. Benches, phones, floorboards, and pretty much anything else a shopper can buy pass through them. Today, America has more warehouses than ever before. But they were surpassed: by lack of workers to get things in and out quickly, due to lack of truck driver and wagons to transport everything – and above all, by an unusual abundance of goods.
“It’s not that the system is broken,” said Zac Rogers, assistant professor of supply chain management at Colorado State University.
Pandemic warehouses are already quite busy, with more than 90% of space occupied. Then factories, docks, and shops began to close. People cut back on shopping and stuff in the warehouse started to pile up. Then, when things opened up again, a flood of goods came rushing in.
“The warehouses are full and now they are really full,” says Rogers. His data shows that available warehouse space has decreased every month since last spring.
Meanwhile, shoppers spent at a record level – freeing up all the money saved by not traveling or going out – and their lurking pandemic anxiety – into shopping for everything. On average every year, online spending can increase by 10% 0 or 15%. Last year, it skyrocketed over 40% and just keep growing until 2021.
Retailers responded to the surge in demand by increasing imports to record levels. Companies scramble to bring in as much of the US as they can, while they can – because they’ve seen the disruptions factories and ports can cause. They started storing things “just in case” shoppers wanted them, instead of “just in time” when shoppers were likely to buy.
“You can basically see this pre-apocalyptic mentality in all of the companies, where normally they’ve been as lean as possible,” says Rogers.
Warehousing companies have been building as fast as possible. In fact, it was a type of commercial building that boomed through the pandemic.
But setting up millions of square feet with conveyor belts, robots and all the bells and whistles takes time. In addition, the main warehouse space is difficult and limited.
Building a barn usually involves finding a cornfield in the suburbs, or aligning with a freeway intersection, Kiersey says. Now, that’s too far. Retailers want to get packages delivered to their doorstep in the shortest possible time, which means fast shipping for storage in expensive and crowded urban and suburban areas.
Warehouse builders are just calculating all of that as the explosive shopping pandemic raises the stakes.
“So demand went against the static supply,” says Kiersey.
In just one year, warehouse rents in some markets have doubled. Brand new buildings that often sit empty for months are selling out before they’re completed. One day, Kiersey had to do the unheard of: turn away a former customer when three companies scrambled for the same warehouse.