Jackson Health saves $1 million with spare parts procurement technology
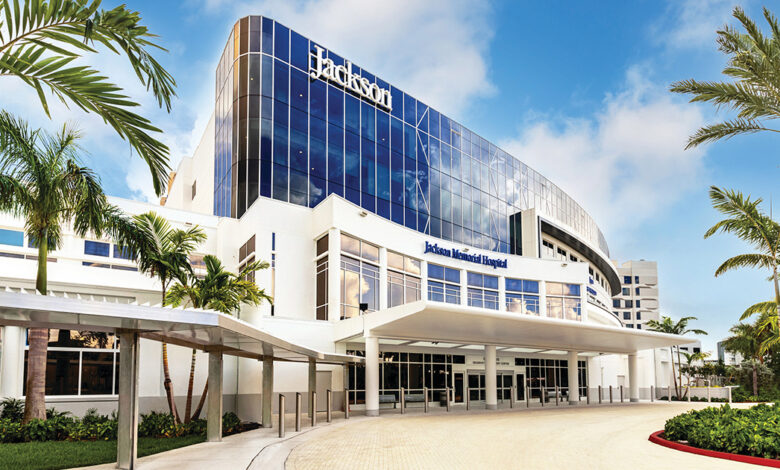
Jackson Health System is one of the nation’s largest public health systems, with a mission to provide a high standard of care to all Miami-Dade County residents, regardless of their ability to pay.
At Jackson, Charles Berberette, director of clinical engineering systems, manages a A team of 29 clinical engineers maintains more than 45,100 medical devices at four hospitals, multiple urgent care centers, and care locations for correction, rehabilitation, transplantation, outpatient, and wellness. behavior.
The Public Health Trustees Committee, founded in 1973 by the County Board of Commissioners, is a group of voluntary citizens that sets policies for Jackson to ensure the health system meets the needs of the community. .
As a civic agency, the group leads joint planning between the Jackson Health System, the University of Miami Miller School of Medicine, Miami-Dade County, and other public and private organizations.
PROBLEM
Berberette identified three issues facing the organization with regard to clinical decision support data technology:
- Procurement of spare parts for medical equipment.
- A work order ticketing system through a computerized maintenance management system.
- Strengthen network security monitoring.
Procurement of spare parts for medical equipment
Jackson had previously encountered challenges with parts procurement and quality, two factors that influenced the decision to bring the clinical engineering team to work in-house in 2019 and create a new paradigm for customer engagement. clinical success.
“The health system wants to work with a supplier that allows us to achieve greater cost savings through more negotiation and stronger purchasing power,” explains Berberette. “A system-wide parts and services procurement platform will promote standardization, improve quality, and improve cost savings and overall efficiency.
“With more than 45,000 medical devices to manage, we also need data to analyze the effectiveness of the parts we use and issues related to cost and quality,” he continued. “We didn’t have that information and knew that our solution had to provide the ability to make data-driven decisions.”
Work order ticketing system via CMMS
Jackson did not have a viable CMMS system nor an efficient way to create a work order system. It needed a computer-based system to integrate financial and time systems, and linked with its CMMS to establish an automated work order system for all employees. CE technicians and service personnel throughout the hospital.
“For example, someone would call the biomed store and tell us about their device problem,” says Berberette. “Our staff will then record the call and incident and find a designated technician to provide that information.
“The technician would then manually create the work order in the system, resolve the situation, service the equipment, and return to our department downstairs to close the work order,” he added.
Jackson is not accountable from a true turnaround time perspective. If a technician forgets to enter a work order during a call, he can create it after the job is done.
So when Berberette looked at the orders, it looked like the job was done in a day, even though the paramedic told us the equipment had been down for three weeks. The organization also does not have staff to answer the phone and assign work to technicians.
Strengthen network security monitoring
Jackson does not have an effective patch management program for its internet health systems. It wants to tackle this challenge and find an AI-powered program.
“This is always the top priority of any health system because Cybersecurity incidents can cause up to $10 million in damage on average, data that I always review when talking about this topic,” noted Berberette. “Anytime you can prevent disruptions in your IT infrastructure, that’s huge. And that’s what we want to do with an AI-powered program.”
PROPOSE
Housekeeper
“Wasting money is my biggest annoyance,” says Berberette. “With Supplier PartsSource, Jackson streamlined his procurement process and worked with one supplier to access a wide variety of products from multiple companies.
He continued: “PartsSource and Jackson also conform to existing quality standards, which means we can depend on getting products ready to use and working properly.” “The parts supplier also completed Jackson’s supplier vetting process, a requirement we follow as a public health system.”
In addition, Jackson wanted to make CE employees more efficient in procuring parts and managing orders. Parts supplier platform provides granular visibility that helps technicians track and track their parts orders, manage internal uptime expectations as well as tracking of core returns and exchanges, which means less time and money wasted in organization.
“And ultimately, quality patient care is our primary goal at Jackson and in the clinical engineering department,” says Berberette. “Knowing that we have access to quality parts through the parts supplier’s platform is also important to meeting clinical needs.”
Job requisition voting system
The CE team linked up with IT business partners and developed software that allowed Jackson to upload databases and asset information to the system. Each property has a technician assigned to it. This is the first step in this process before deploying the system.
“For example, if a clinical staff member has a problem with a device, we enter the information, the asset number, and the part,” explains Berberette. “The system automatically re-links to our CMMS to identify the technician assigned to that part or device.
“It then cross-references the time management system to see if the person is watching the clock,” he continued. “If that person isn’t on the clock, the system checks the extra worker, meaning the system knows who’s working at any given time.”
Jackson also built an escalation tree and set limits for critical and non-critical devices to escalate calls to the next layer of management without human effort. It has an internal process for giving work orders without giving it to someone to make sure the work gets to someone.
Timestamps facilitate an internal process to send work orders to technicians without human interaction.
Network security
“We conducted a risk assessment as an organization and knew we needed an AI-powered solution linked to the medical device to be able to identify vulnerabilities,” Berberette revealed. latent. “We wanted a more efficient tool to check for vulnerabilities, such as necessary patches for devices.
He continued: “The introduction of an AI-based solution to address cybersecurity challenges was a first for Jackson. “Vendor Cynerio has helped protect Jackson’s medical equipment against cybersecurity threats, including IoMT equipment.”
MEET CHALLENGES ONLY
Housekeeper
The entire medical system and its thousands of patients depend on the CE team to maintain the clinical availability of critical medical devices. Jackson employees know that any disruption in service resulting in equipment downtime is not an option.
“We introduced PartsSource Pro, their managed service model that combines cloud-based data analytics, best practices, and logistics support to make informed decisions,” explains Berberette. evidence for the procurement of parts and services”.
“The supplier system saves costs and helps drive process efficiency,” he continued. “For example, the platform will automatically send return and core exchange reminders to the technician to order and the paperwork is self-serviced directly from the website.”
Job requisition voting system
Jackson built in-house CMMS software to ensure regulatory compliance and operational efficiency from the outset of this new program.
For example, if a clinician has a problem with a device, the staff member will enter that information, the asset number or even the part to link it back to the CMMS system automatically, to see who gets referred. assigned to that part or that part. that piece of equipment as a primary.
“It then refers to Kronos, our workforce management system, to see if the person is tracking time,” explains Berberette. “Otherwise, the system will text the technician on duty. If that person isn’t on duty or has been off that day, the system checks the sub technician to see if they’re on or off the meter. “
That means employees will know who is available at any given time, and the system will allow employees to effectively hand off work to the right people. Jackson also sets limits on critical or non-critical equipment to automatically escalate calls to the next layer of management without human interaction. All orders have timestamps and progress notes for easy access by technicians.
RESULT
Jackson saved $1 million annually from 2019 to 2022 on spare parts purchases.
“The more efficient we are at work and the faster the equipment turnaround, the more devices we have available to patients, which reduces hospital stays and increases patient satisfaction,” says Berberette. “Our savings over these four years are consistently based on the use of a data-driven decision-making platform from PartsSource.
“I’m always looking for process improvements to drive the success of my team, knowing that every decision impacts Jackson as an organization,” he continued. “Suppliers monitor quality margins by tracking returns on all items from all suppliers. PartsSource’s current quality return rate is 0.48%. Our quality return rate target is 0.5%, which equates to a 99.5% quality acceptance rate.
By using suppliers for fiscal year 22 (October 2021 to October 2022), Jackson’s component procurement spending would be 46% higher than if Jackson purchased components himself. By using spare parts supplier, it can save 34% compared to market price when buying spare parts.
“In addition, PartsSource managed 1,850 medical device orders on our behalf; this allowed us to consolidate 202 suppliers, another example of effective management based on our procurement model. us,” Berberette noted.
TIPS FOR OTHER PEOPLE
“Start with a needs assessment and develop a scope of work that allows clinical technicians to work the way they need them to in their organization,” advises Berberette. “This includes looking at technologies and partnerships that allow them to maximize efficiency and financial stability.
He continued: “Then consider the needs of your organization and look for areas of opportunity that encourage growth. “Consider past problems and challenges, and then strive to develop solutions, especially computer-based, repeatable and self-sufficient solutions, to help develop content programs.” your set.”
He concluded, with cybersecurity, choosing the best solution for an organization is always the most effective, but at the same time constantly looking for areas for improvement that can bring the organization more efficiency. more in that area, he concluded.
Follow Bill’s HIT coverage on LinkedIn: Bill Siwicki
Email the writer: [email protected]
Healthcare IT News is a publication of HIMSS Media.